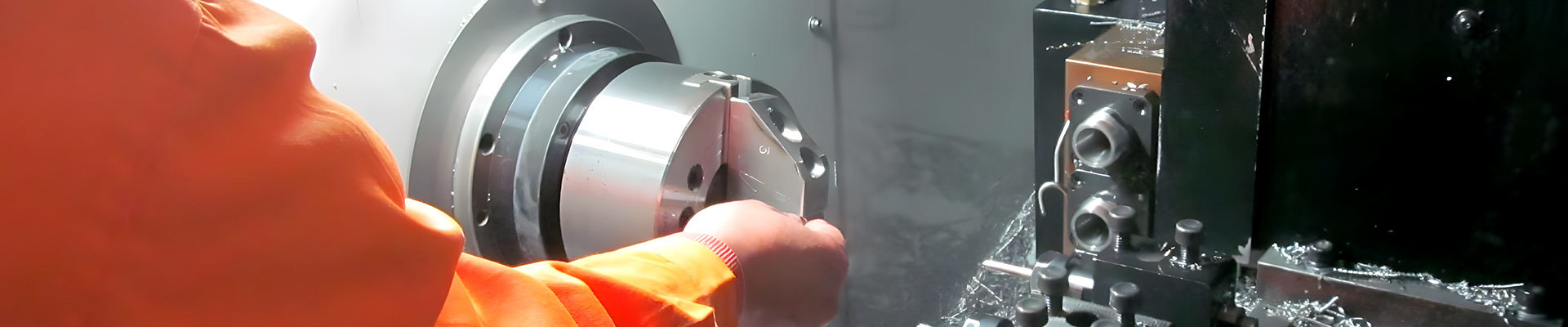
A Comprehensive Analysis of Bearing Basics: The "Precision Heart" of the Mechanical World
In the operation of mechanical equipment, Bearing plays a crucial role. It is like the joints of the human body, supporting rotation, reducing friction and transmitting power. It is the "precision heart" that ensures the efficient and stable operation of machinery. Whether it's car engines, wind turbines or household washing machines, bearings can be found everywhere.
I. The Core Function of Bearings
The core functions of bearings can be summarized in three points:
1. Supporting rotating bodies: Bearing the weight of shafts or rotating parts and external loads;
2. Reduce friction: Replace direct friction with rolling or sliding to enhance efficiency;
3. Precise positioning: Ensure that the rotating parts operate stably along the predetermined trajectory.
Without bearings, direct friction between mechanical components would rapidly generate high temperatures and wear, significantly shortening the equipment's lifespan and even causing malfunctions.
Ii. Classification and Mainstream Types of Bearings
Bearings can be classified into two major categories based on their working principles: rolling bearings and sliding bearings. The two differ significantly in structure, performance and application scenarios.
1. Rolling bearings: Synonymous with efficiency and precision
Rolling bearings achieve rolling friction through rolling elements (balls, cylinders, cones, etc.), featuring low friction coefficients, small starting resistance, and high standardization. They are widely used in modern machinery.
· Advantages: Standardized production, convenient maintenance, and low friction;
· Disadvantages: Sensitive to impact loads and slightly noisy.
2. Sliding bearings: Guardians of heavy load and durability
Sliding bearings operate by sliding friction, have no rolling elements, and have a simple structure. They are suitable for low-speed, heavy-load or high-precision scenarios.
▶️ Common types and characteristics:
· Radial sliding bearing: Supports radial loads
Such as engine crankshaft bearings;
· Thrust sliding bearing: Withstands axial thrust, such as the main shaft of a water turbine;
· Hydrodynamic bearing: Utilizing oil film/gas film to form non-contact support (for high-speed precision machine tools); · Self-lubricating bearings: Containing materials such as graphite /PTFE, maintenance-free (for food machinery and high-temperature environments)
· Advantages: Strong load-bearing capacity, impact resistance, and low noise;
· Disadvantages: High starting friction, requires a lubrication system, and has relatively high maintenance costs.
Iii. Bearing Selection Guide: Four Key Factors
1. Load type and magnitude
· Radial load is the main type → deep groove ball bearings, cylindrical roller bearings;
· Axial load is the main type → thrust ball bearings, tapered roller bearings;
· Combined load → angular contact ball bearings, self-aligning roller bearings.
2. Speed requirements
· High-speed (such as electric spindles) → Deep groove ball bearings, angular contact ball bearings;
· Low-speed and heavy-load (such as mining machinery) → sliding bearings, cylindrical roller bearings.
3. Working environment
· High-temperature/Corrosive environment → Ceramic bearings, stainless steel bearings;
· Dust/Damp environment → Sealed bearing, self-lubricating bearing.
4. Installation and maintenance conditions
· Space limitation → Thin-walled bearings;
· Frequent disassembly required → detachable tapered roller bearing.
V. Practical Tips for Extending Bearing Life
1. Lubrication management: Select grease or oil for lubrication based on working conditions and replenish or replace them regularly.
2. Dust-proof sealing: Install sealing rings or dust-proof covers to prevent impurities from entering.
3. Avoid overloading: Overloading operation will accelerate and cause fatigue failure.
4. Precise installation: Use professional tools to avoid deformation caused by knocking.
VI. Future Trends: Intelligence and New Materials
With the development of Industry 4.0, bearings are evolving towards intelligence (with built-in sensors to monitor temperature and vibration) and material innovation (ceramics, carbon fiber composite materials), further breaking through performance bottlenecks under extreme working conditions.
Although bearings are small, they are the "invisible heroes" of mechanical systems. Correct selection and scientific maintenance can not only enhance equipment efficiency but also help enterprises reduce costs and increase efficiency.