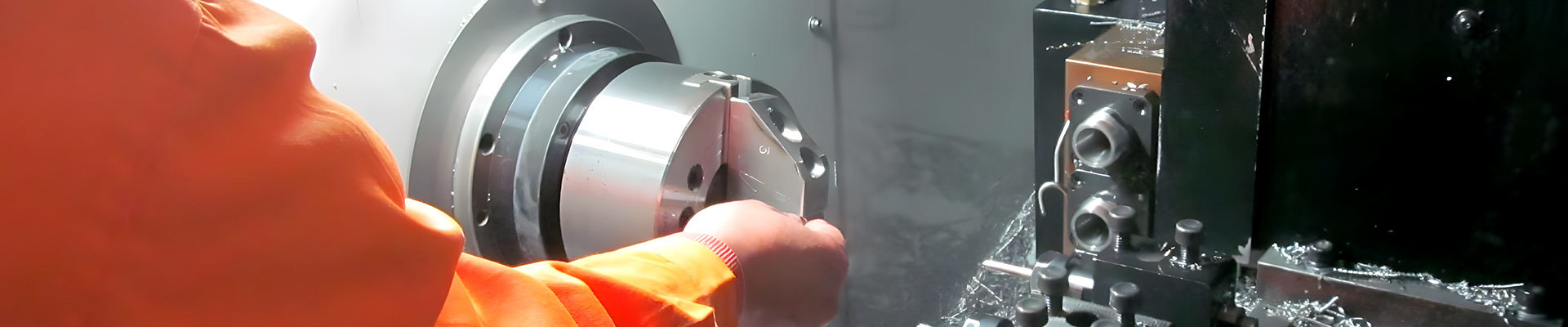
Analysis of the Reasons for the high Temperature of the heart pump bearing
1. Lubrication factors
1.1 Improper quality or quantity of lubricating oil (grease)
1) Deterioration of oil quality: Oxidation, contamination (mixing of water and particles), or long-term lack of replacement of lubricating oil lead to a decline in lubrication performance. 2) Insufficient oil: Insufficient grease filling (less than 1/3 to 1/2 of the bearing cavity) or the lubricating oil level is too low to form an effective oil film. 3) Excessive oil: Over-lubrication causes the stirring to heat up (especially for high-speed bearings). 4) Incorrect oil selection: too high viscosity (poor fluidity) or too low viscosity (insufficient oil film strength), not matching the pump's speed and load.
1.2 Failure of the lubrication method
1) Oil pump failure, pipeline blockage or decreased cooling efficiency of the cooler in the forced lubrication system. 2) The oil ring (oil ring lubrication) gets stuck or falls off, resulting in the bearing not being well lubricated.
2. Mechanical factors
2.1 Defects of the bearing itself
1) Bearing wear, fatigue spalling, cage damage or improper clearance adjustment (such as excessive preload of angular contact bearings). 2) The wrong bearing model was selected (such as insufficient load capacity or mismatched speed grades).
2.2 Poor alignment
The alignment deviation between the pump shaft and the motor shaft is out of tolerance (excessive radial/angular deviation), causing the bearing to bear additional loads. 2) The compensation capacity of the coupling is insufficient or the thermal expansion offset of the rigid coupling has not been corrected.
2.3 Shaft bending or rotor imbalance
Shaft deformation (improper transportation or installation) or excessive dynamic balance of the impeller can cause vibration and be transmitted to the bearing.
2.4 Assembly or fit tolerance issues
1) The bearing is installed too tightly (with excessive interference) or too loosely (causing the ring to run off). 2) The roundness/coaxiality of the bearing housing hole exceeds the tolerance, or the bolts of the bearing box end cover are not tightened evenly.
3. Operating condition factors
3.1 Overload Operation
1) The pump operates for a long time under conditions deviating from the design (such as high flow rate and low head), resulting in an increase in axial or radial force. 2) The balance disc/balance drum of the multistage pump failed, and the unbalanced axial force was transmitted to the thrust bearing.
3.2 Excessive Vibration
Cavitation, surging or unstable inlet flow (such as a too close elbow) can cause high-frequency vibration, accelerating bearing wear.
3.3 Insufficient Cooling
The fan failure of the air-cooled bearing or the scaling/clogging of the water-cooled sleeve leads to a decrease in heat dissipation efficiency.
4. External environmental factors
4.1 Temperature Conduction
The heat of the high-temperature medium is conducted to the bearing box through the pump casing or shaft (if no insulation measures are designed).
4.2 Intrusion of Pollutants
Dust, moisture or corrosive media entering the bearing cavity can damage the lubrication or directly wear the bearing.
4.3 Insufficient rigidity of the foundation
Pipeline stress or foundation vibration is transmitted to the pump body, causing the bearings to bear additional loads.
5. System design issues
5.1 Improper selection of bearings
1) Load calculation errors result in insufficient rated dynamic load of the bearing.
2) Angular contact bearings, ceramic bearings or sliding bearings were not selected under high-speed working conditions.
5.2 Design flaws in the cooling/lubrication system
The grease injection path/lubricating oil circuit design is unreasonable or the cooling capacity is insufficient (such as no forced cooling configuration in high-temperature conditions).
6. Suggestions for fault diagnosis process
6.1 Preliminary Inspection
Confirm the lubrication status (oil level, color, contamination degree), noise and bearing vibration value.
2) Check the temperature distribution of the bearing housing (local overheating may indicate installation issues).
6.2 Analysis of Operating Parameters
Compare historical data to confirm whether there are any abnormalities in flow, pressure or current.
6.3 Disassemble and inspect the certificate
Check the wear marks of the bearings (such as pitting and adhesive wear), centering data and sealing integrity.
7. Solutions and Preventive Measures
7.1 Lubrication Management: Regularly replace the lubricating oil (grease) as required in the supplier/manufacturer's documentation, and use an oil quality analyzer to monitor the deterioration trend.
7.2 Alignment Correction: A laser alignment instrument is used, and thermal expansion compensation is taken into consideration. 7.3 Vibration Control: Regular dynamic balance calibration and optimization of the inlet pipeline design.
7.4 Working Condition Monitoring: Install online monitoring systems for temperature and vibration to achieve early warning. By systematically investigating the above factors, the problem of high bearing temperature in centrifugal pumps can be effectively solved, and the service life of the equipment can be prolonged. In practical applications, targeted analysis should be conducted in combination with specific working conditions and equipment structure.